Delamination and impact resistant composite materials using nanofiber toughening veils
Unbreakable composites using nanofibers
New toughening technology increases the delamination and damage resistance of composites up to 200% without any increase in mass. It is based on the incorporation of tough nano- and microfiber non-woven veils in between the reinforcing plies of the composite material.
Fiber reinforced polymer (FRP) composite materials are already a go-to engineering material in industries like aerospace or wind energy, but their poor delamination and impact tolerance remains a problem for many applications. Our research has proven that interleaving toughening veils that are based on electrospun polymer nanofibers or microfibers is a very efficient technique to create delamination and damage resistance. By incorporating the toughening veils, the weak and brittle interlaminar region between the reinforcing plies becomes very tough, which in turn toughens the composite as a whole. Our results show improvements of the delamination resistance up to 200%, a 50% increase of the Barely Visible Impact Damage limit and a 50% reduction in internal damage produced by low-velocity out-of-plane impact events.
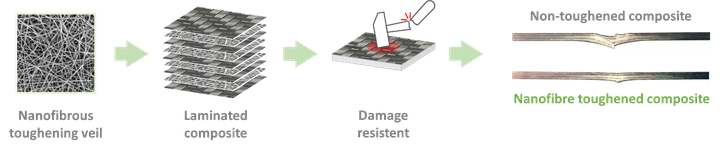
Adding nano- and microfibrous toughening veils is thus a very effective way of increasing the damage resistance of the composites without negatively affecting other mechanical properties. These veils can either be incorporated as stand-alone membranes (high permeability veils pose no problem for resin infusion) or even directly deposited during the electrospinning process onto the reinforcing plies themselves. As such, these materials are much easier to integrate into current production routes and parts in comparison to other toughening nanotechnologies such as graphene or carbon nanotubes. Furthermore, they pose no health hazards as they come as a flexible bulk membrane while the fibers themselves are continuous and their diameter (100 – 1000 nm) is large enough to not penetrate the human body through contact.
The toughening veils can be made from a wide range of polymers. We have successfully used polycaprolactone, polyamides, polyesters and several commercially available co-polymers. The veils are produced through electrospinning and can be manufactured continuously either as a stand-alone product or deposited onto existing reinforcing plies or other carrier structures. After composite consolidation, the nanofibers are embedded in the matrix material and act as crack stopping agents. They are inherently tough and well suited to absorb impact energy, for example from tool drops, hail or other collisions.
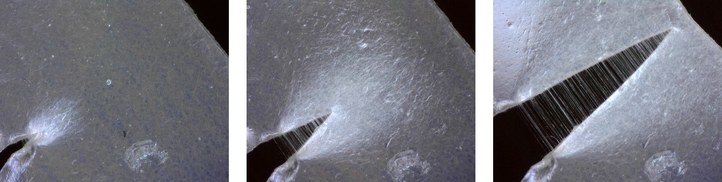
This research is performed in co-operation with the Mechanics of Materials and Structures research group led by professor Wim Van Paepegem which is specialized in composite testing. The materials have been tested for their delamination resistance under static and fatigue loading, low-velocity impact resistance, compression after impact strength, tensile/flexure/shear properties, etc.
Further information
Acknowledgements
- Bijzonder Onderzoeksfonds Universiteit Gent (BOF 13/24J/020, BOF.EXP.2017.0007, BOF/STA/202009/046)
- FWO Vlaanderen (IWT SB 141344, 12ZR520N)
Contact
Prof. dr. ir. Karen De Clerck (Karen.DeClerck@UGent.be)
Prof. dr. ir. Lode Daelemans (Lode.Daelemans@UGent.be)